Production Inventory¶
Production Inventory is used to view current Inventory levels of a particular Item, as well as all transactions that transpired for an Item to get to its current Inventory level. A user can verify both Inventory counts which include Tag Inventory and Production Inventory.
To view the Production Inventory screen, navigate to the tab and click on the
icon.
This will open the Production Inventory screen.
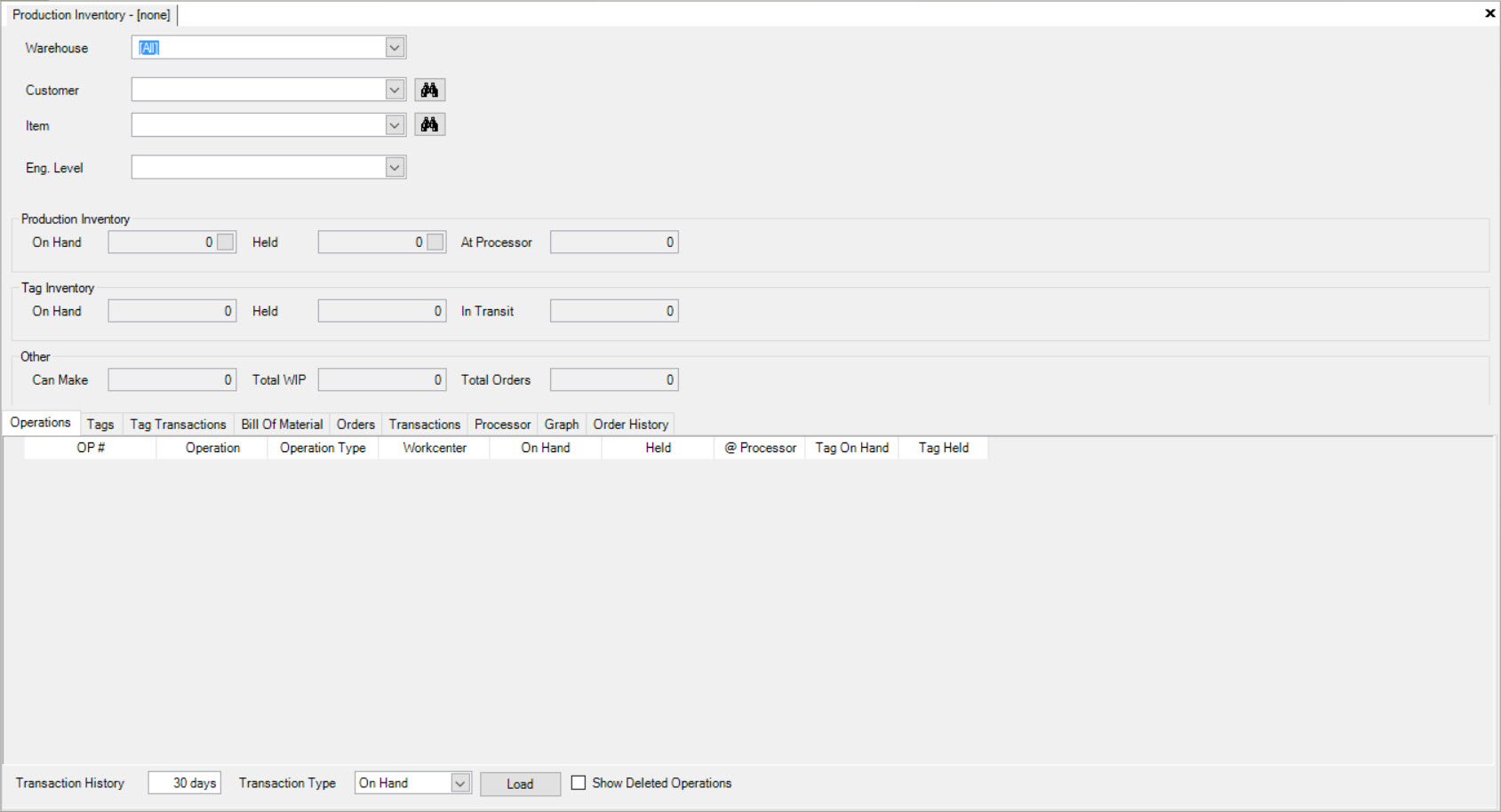
Select a Warehouse, Customer, Item, and/or Eng. Level using the drop-down menus. Users can also click on the button to find a Customer
or Item.
Once you have entered or selected the appropriate fields, the Inventory Counts will be populated in the system (if they exist).
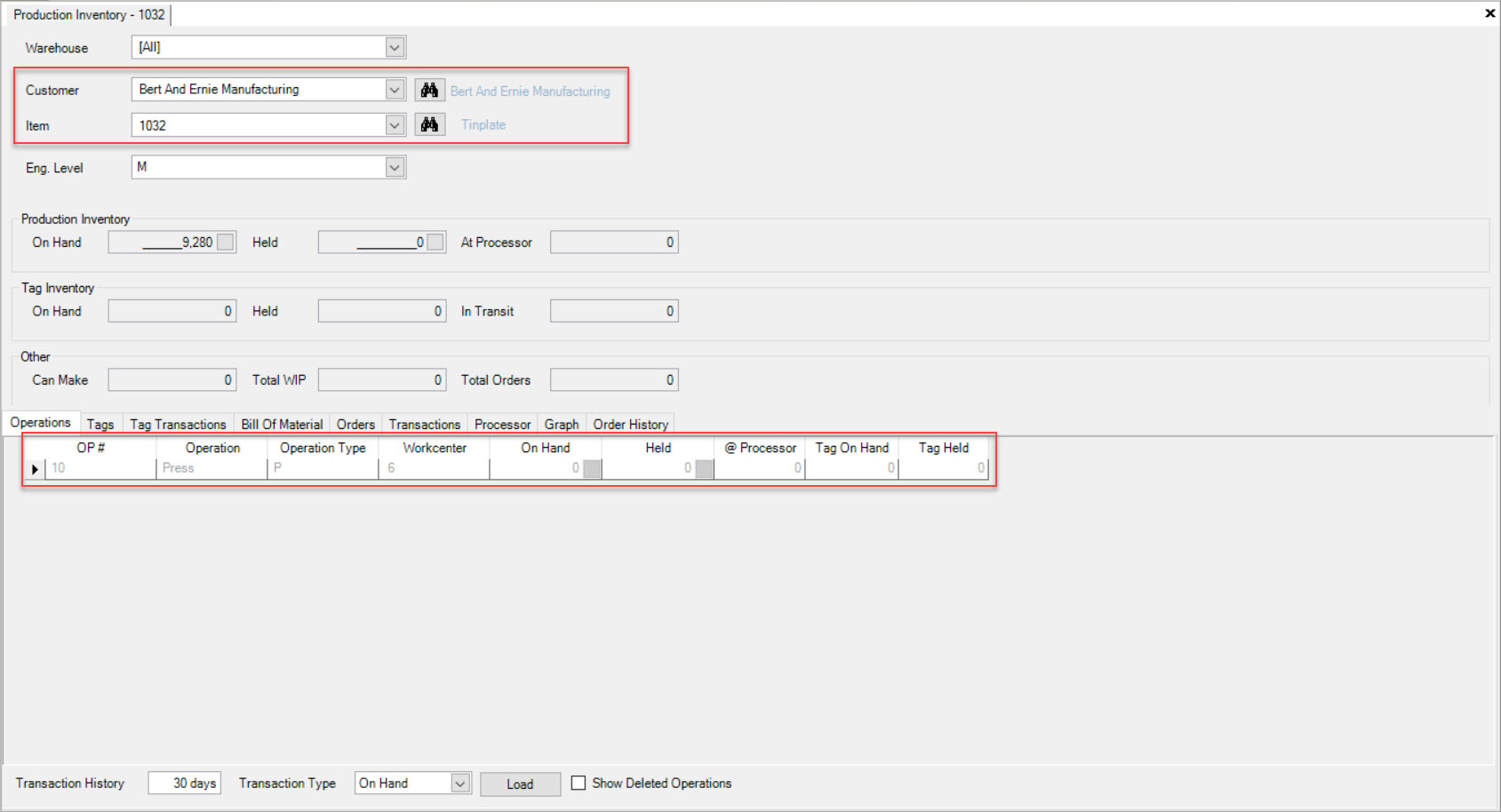
Note
The Quantities located at the top of the screen under Production Inventory, Tag Inventory, and Other reflect Finished Goods only. If users want to adjust On Hand Operations or Processor WIP, the adjustments will not be reflected under these Quantities.
Production Inventory Header¶
There are three options under the Production Inventory header: On Hand, Held, and At Processor.
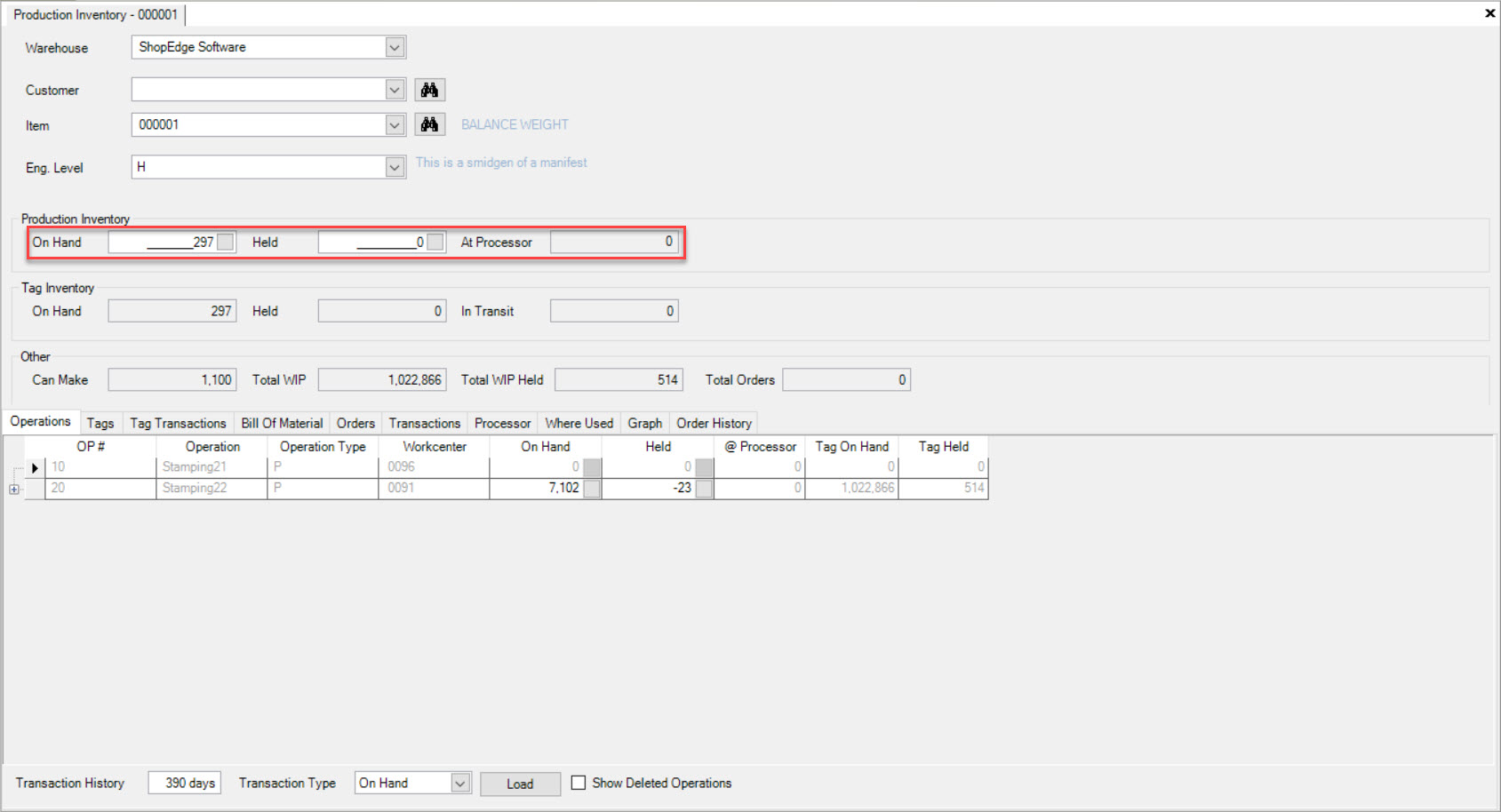
Production Inventory is updated by transactions like Receipts, Timecard Entries, Shipped Packing Slips, Cycle Counts, and Inventory Adjustments.
The system will show the current Finished Good inventory quantities for On Hand, Held, and At Processor inventories. To see WIP (Work in Progress) information for each of the
same categories, view the tab below.
Tag Inventory Header¶
There are three options under the Tag Inventory header: On Hand, Held, and In Transit.
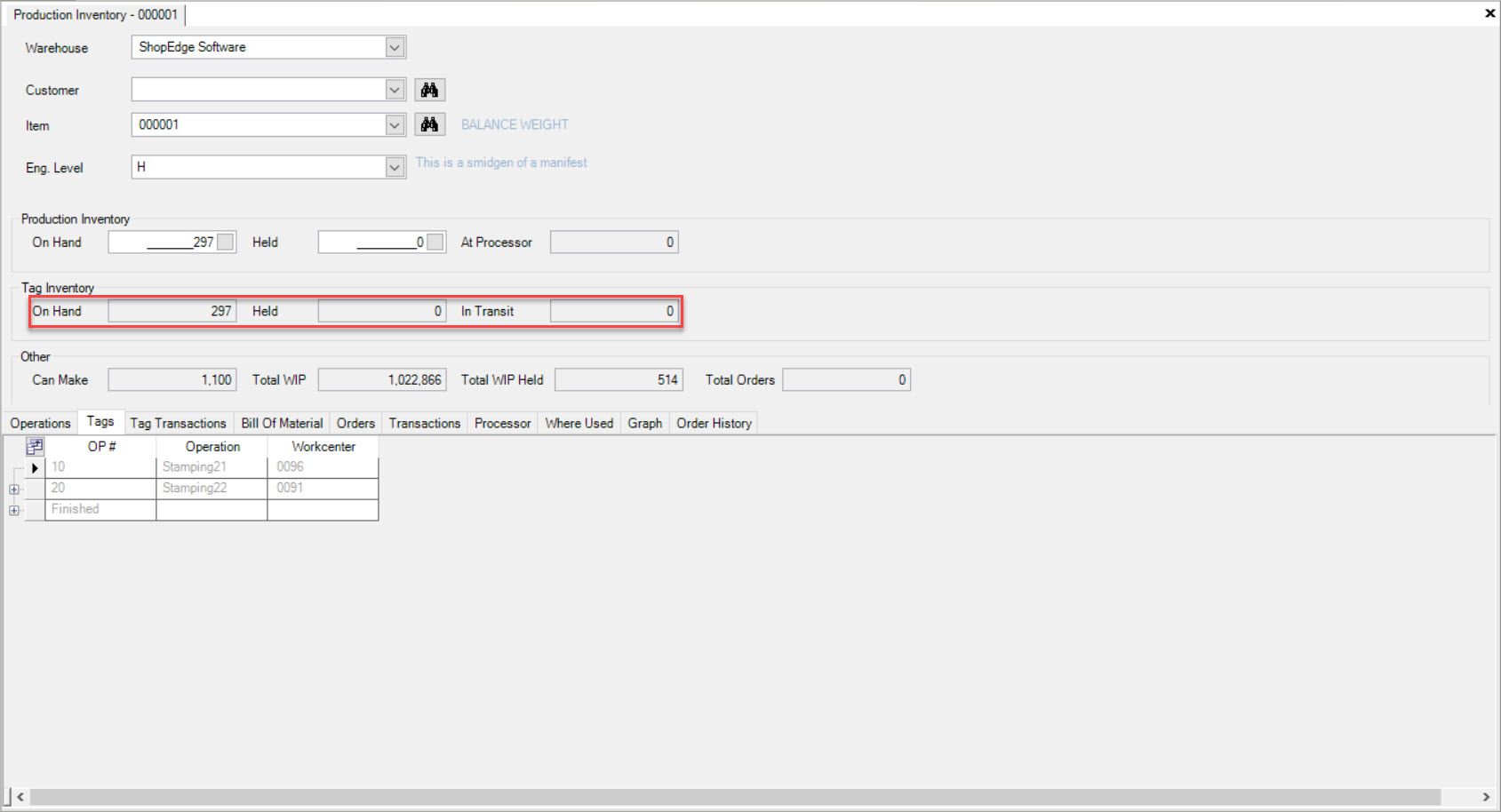
Tag Inventory is updated by transactions like Serial Numbers created when performing a Receipt, shipping Serial Numbers on a Packing Slip, modifying a quantity on a Serial Number, consuming a Serial Number, and creating or deleting a Serial Number.
The system will show the Finished Good inventory quantities for On Hand, Held, and In Transit inventory. To see WIP (Work in Progress) information, view the
tab.
Other Header¶
There are three options under the Other header: Can Make, Total WIP, Total WIP Held, and Total Orders.
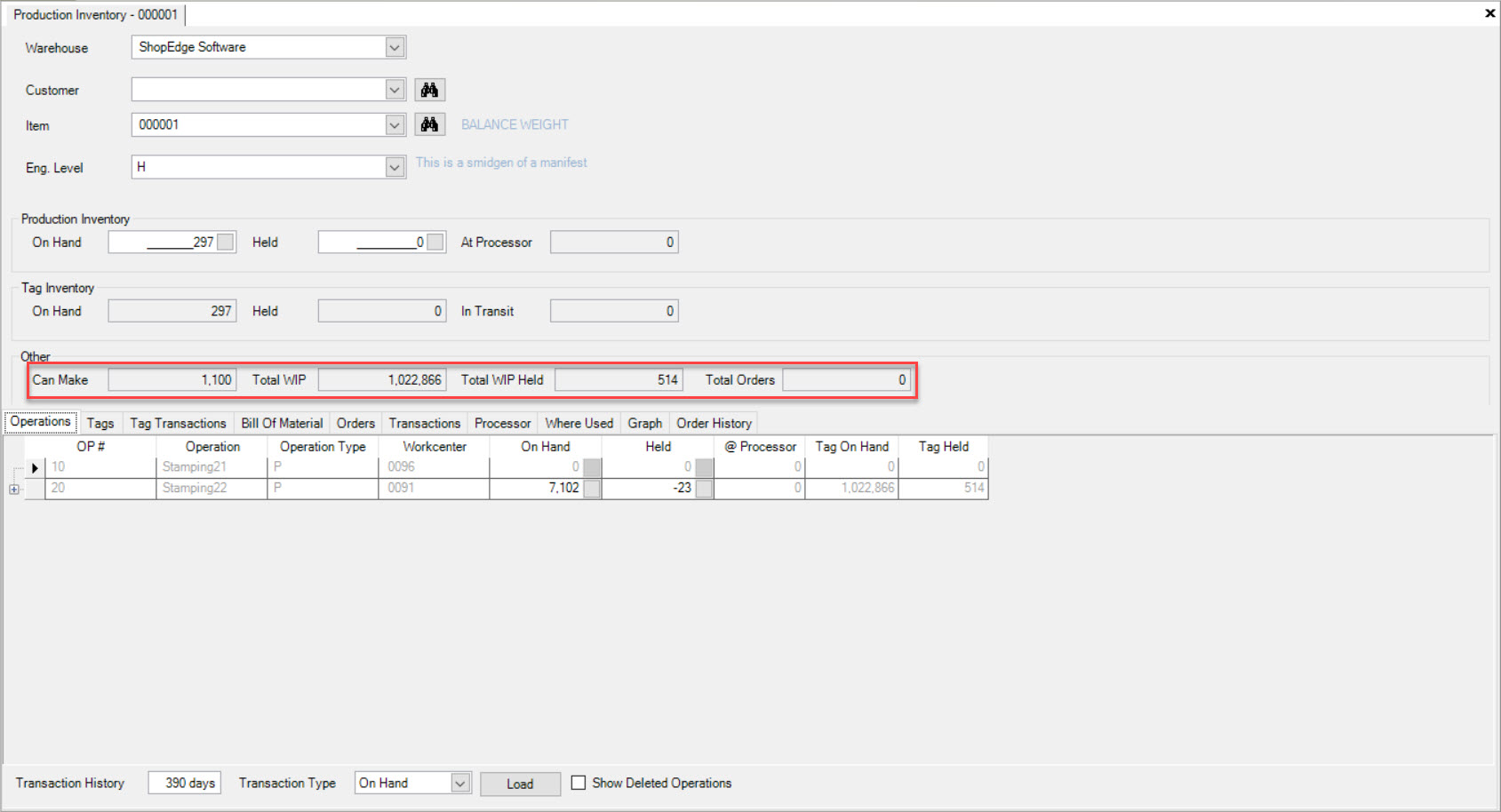
The Can Make quantity is related to the inventory on the tab for the operation 10 of the Item.
The Total WIP is the quantity of combined WIP for the Item, which includes outside processor inventory and all inventory that is not Finished Good inventory.
The Total WIP Held is a sum of all WIP quantities that have a current Held status.
The Total Orders is a sum of the Orders (Firm or Planned) in the tab below.
Inventory Adjustments¶
Before making an Inventory Adjustment, make sure to select a Warehouse. This step is to ensure that the ShopEdge system knows which Warehouse Location to apply the adjustment to. Once this step has been done, the Production Inventory On Hand and Held fields will be available to click on.
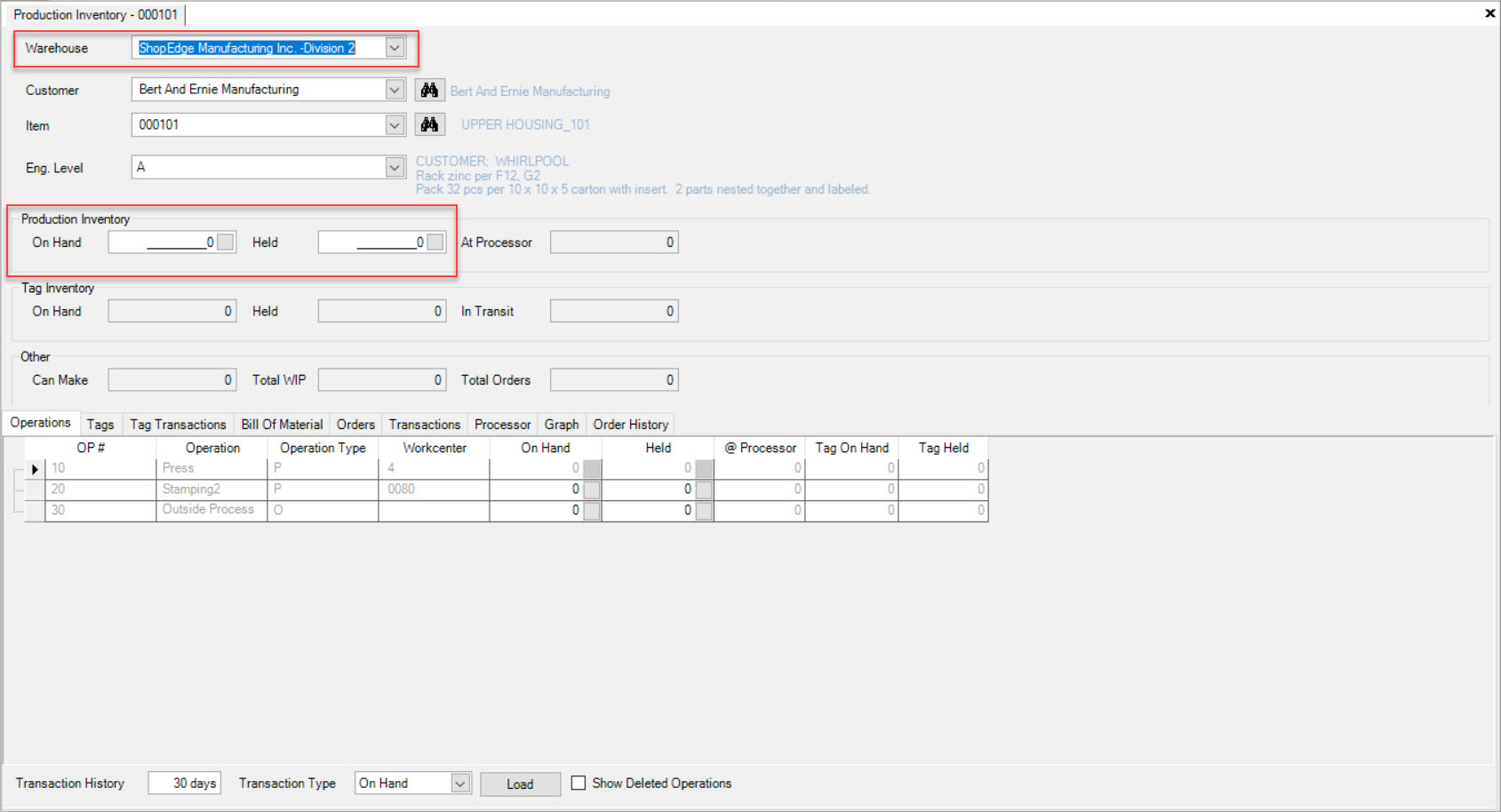
On Hand Adjustments¶
To make an On Hand adjustment, click on the button beside the Production Inventory On Hand field. The Inventory Adjustment window
will appear.
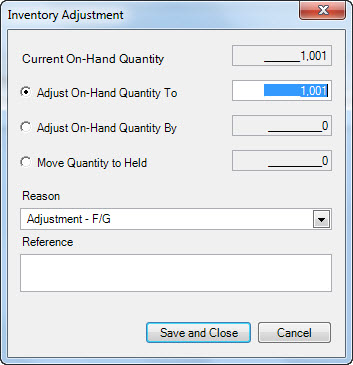
Users can select Adjust On Hand Quantity To, Adjust On Hand Quantity By, and Move Quantity to Held. When one is selected, the appropriate textbox will be available to enter in an amount. Once an amount is entered, select a Reason by using the drop-down menu provided and enter in a Reference if necessary.
Click on the button to complete the adjustment.
Note
Under the tab, users can adjust inventory quantities for both On Hand and Held inventory for WIP (Work in Progress), the same way as explained above. Make sure the
tab is selected, and click on the grey box in the On Hand or Held columns to view the Inventory Adjustment window.
Held Adjustments¶
To make a Held adjustment, click on the button beside the Production Inventory Held field. The Inventory Adjustment window will appear.
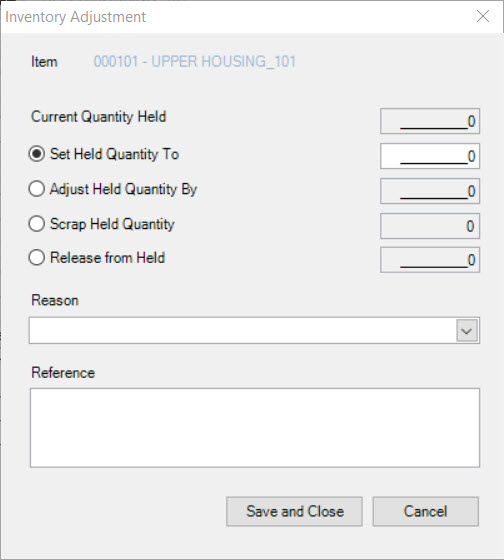
Users can select Set Held Quantity To, Adjust Held Quantity By, Scrap Held Quantity, and Release from Held. When one is selected, the appropriate textbox will be available to enter in an amount. Once an amount is entered, select a Reason by using the drop-down menu provided and enter in a Reference if necessary.
Click on the button to complete the adjustment.
Note
Under the tab, users can adjust inventory quantities for both On Hand and Held inventory for WIP (Work in Progress), the same way as explained above. Make sure the
tab is selected, and click on the grey box in the On Hand or Held columns to view the Inventory Adjustment window.
Tag Adjustments¶
Users have the ability to delete Tags on the Production Inventory screen, but are unable to create new Tags.
To delete a Tag, make sure to select the tab.
Locate the Tag you wish to delete and highlight the appropriate row. Use your Delete key. The Inventory Adjustment window will appear where users must select a Reason,
enter in a Reference, and then click on the button.
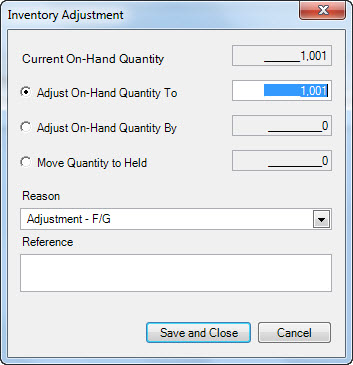
Make sure to save your changes before exiting the screen.
Note
To create a Tag in the system, please see Shipping > Inventory.
Operations Tab¶
The Operations tab on the Production Inventory screen will be selected by default when the screen is first opened.
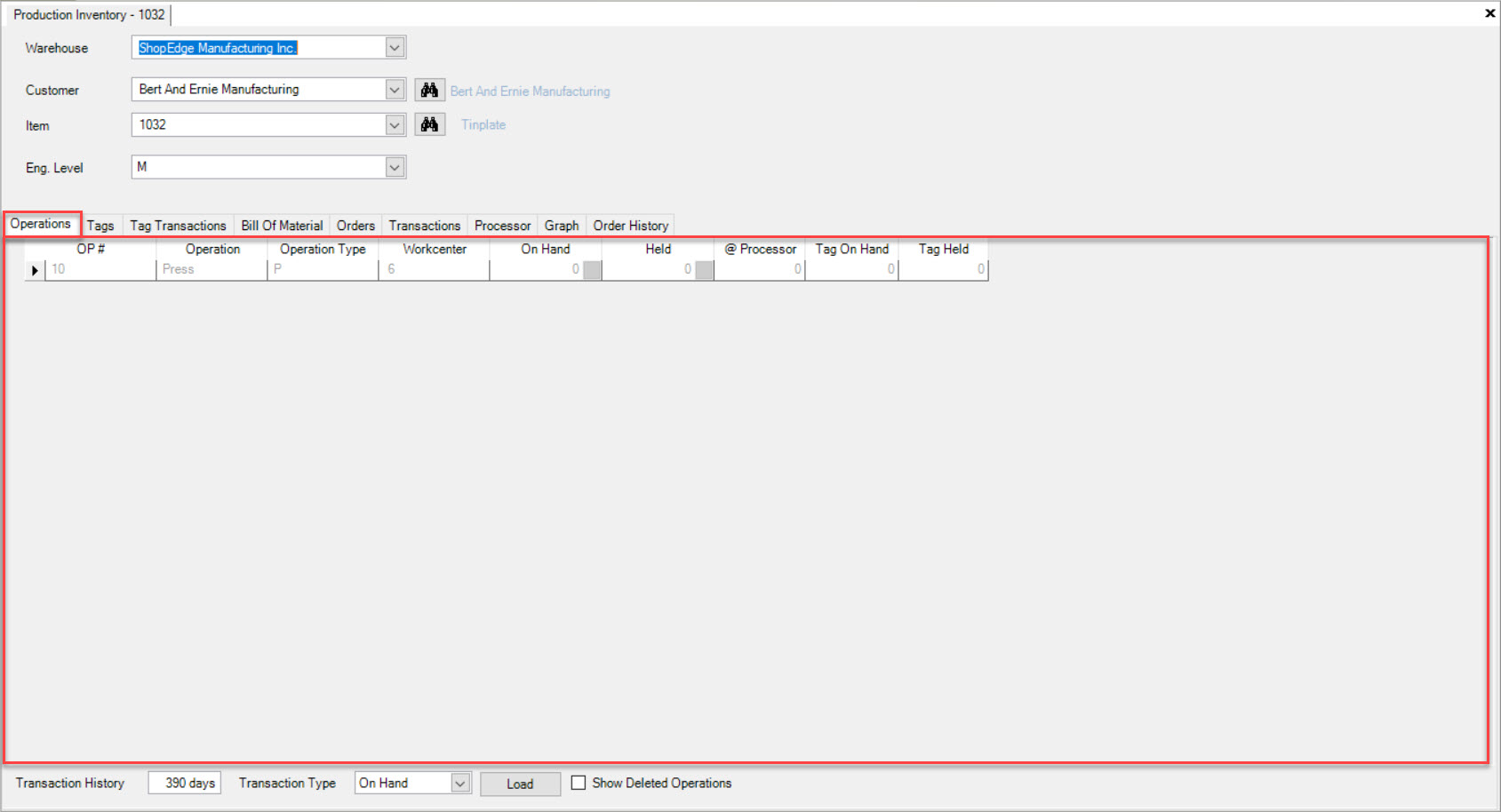
This tab is useful for viewing all Operations, as well as Inventory quantity (On Hand, Held, @ Processor, Tag On Hand, and Tag Held) for each Operation.
The user has the option of adjusting On Hand or Held inventory quantities at each Operation as well. You can expand each Operation (if there is a + beside it) to see the Transactions that took place in order to get to the current Inventory position.
Users also have the ability to view the Transaction History as far back as you wish. Simply enter in the number of days, select the Transaction Type from the drop-down and click on the
button.

Note
Users can select or de-select checkbox if necessary.
Tags Tab¶
The Tags tab on the Production Inventory screen can be viewed by clicking on the tab.
This tab is useful for viewing all Operations, the On Hand Tags and Serial Numbers at each Operation.
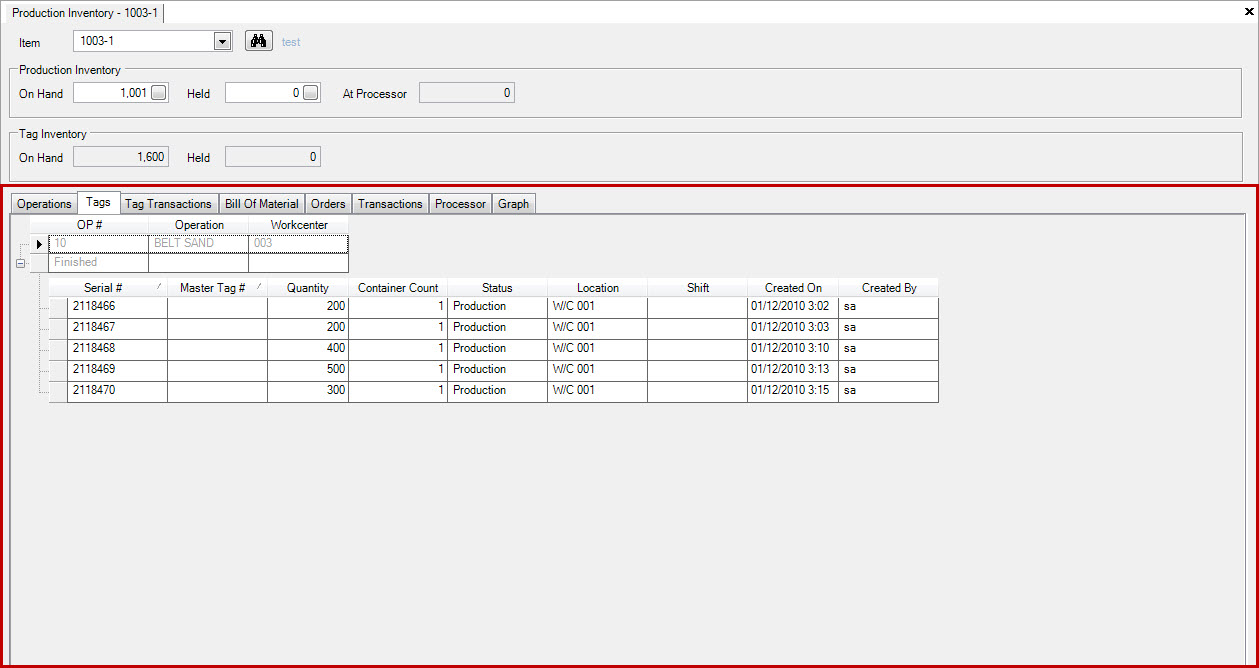
Users can also open the Manufactured Item Tag detail screen by double-clicking on the appropriate row or by right-clicking on the appropriate row and selecting the View Details option. The Manufactured Item Tag detail screen will be displayed.
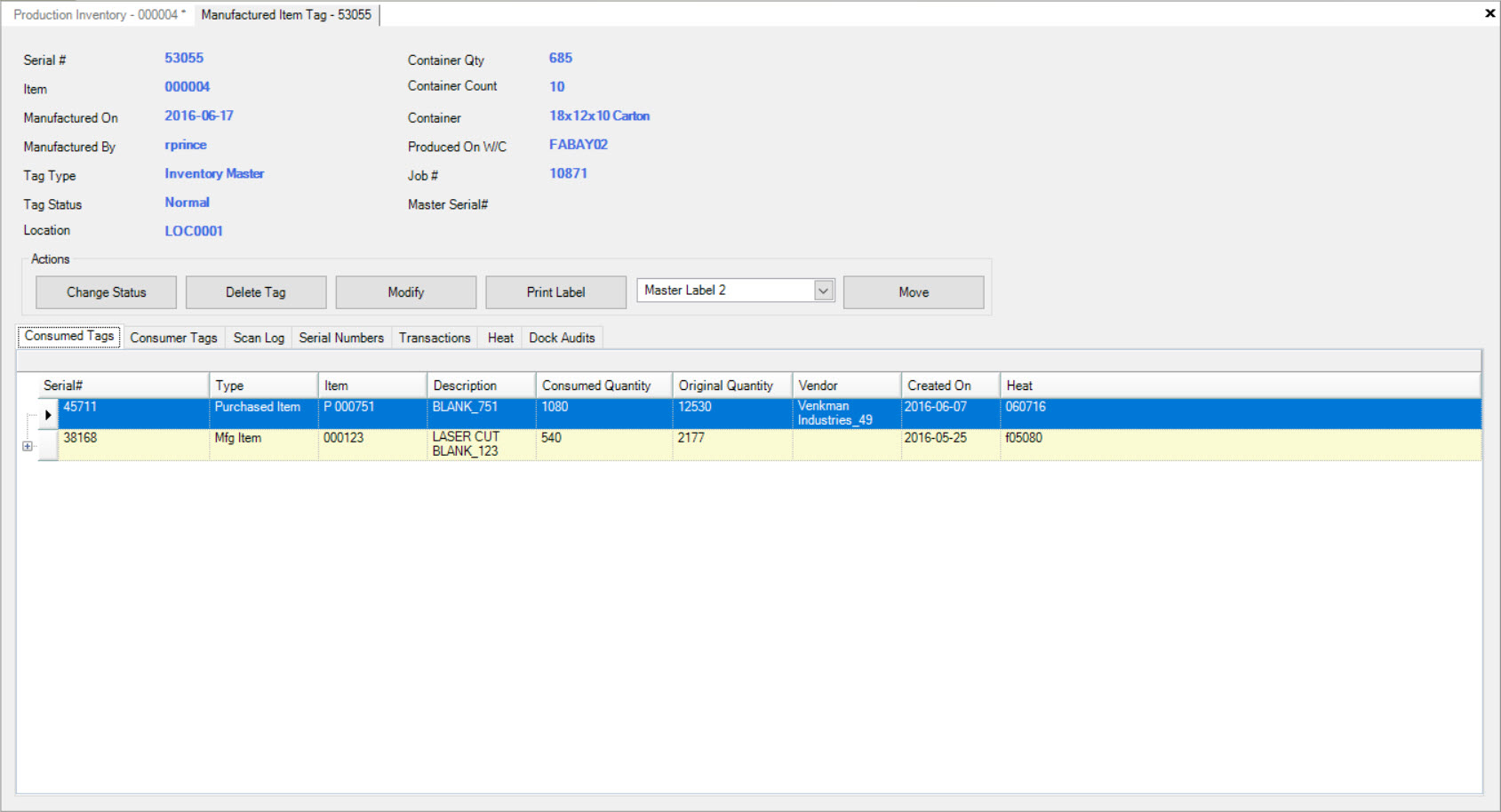
Users are able to change the Tag Status, modify or delete the Tag, print a new label, or move the Tag to a new Warehouse and Location. Users can also view various transactions related to the Serial Number on the screen.
Note
For more detailed information on the Manufactured Item Tag detail screen, please see Quality Assurance > Manufactured Item Tag Lookup.
Tag Transactions Tab¶
The Tag Transactions tab on the Production Inventory screen can be viewed by clicking on the tab.
This tab is useful for viewing all Operations, and the On Hand Inventory Tag quantities and transactions from scanning.
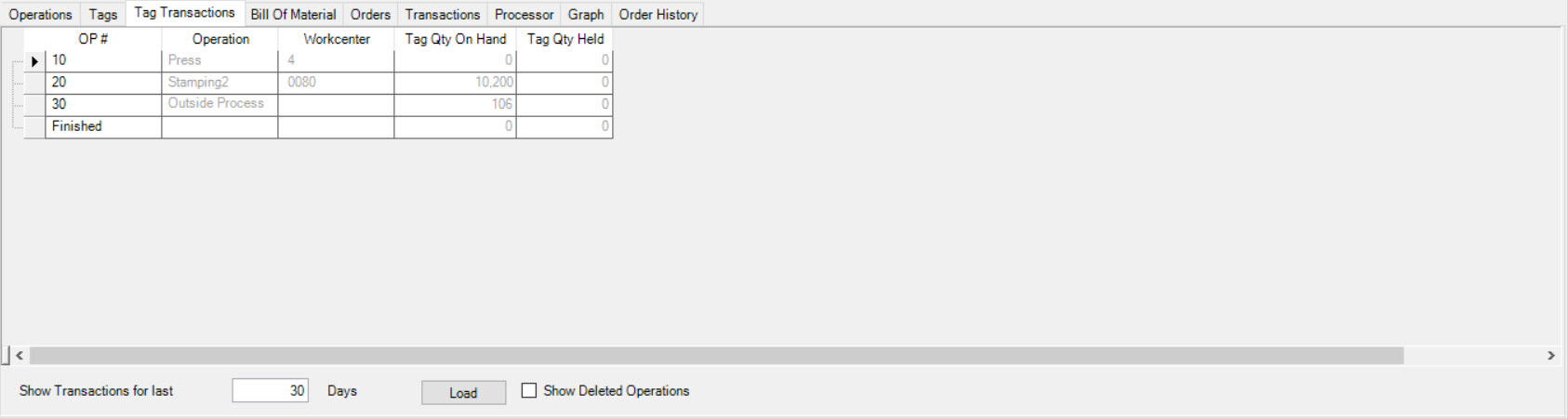
Users also have the ability to view the Transaction History as far back as they wish. Simply enter in the number of days and click on the button.

Note
Users can select or de-select checkbox if necessary.
Bill of Material Tab¶
The Bill of Material tab on the Production Inventory screen can be viewed by clicking on the tab.
This tab is useful for viewing Bill of Material information for each Item.
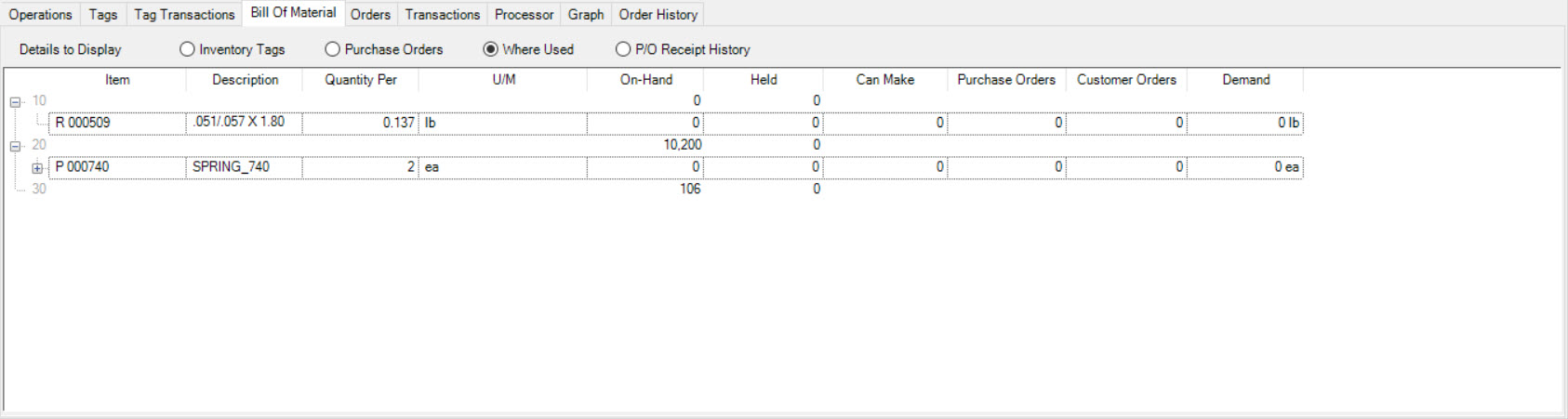
Users can select which details they wish to view for the Operations listed below. Options include:
- Inventory Tags: shows a combined total of On Hand Tag quantities for each Bill of Material Item. It also includes On Hand, Held, Can Make quantities, Open P/O’s, Customer Orders, and Demand quantities.
- Purchase Orders: shows open Purchase Orders for each Bill of Material Item including the P/O #, Vendor, Wanted On date, Open Quantity, U/M, and Can Make.
- Where Used: shows if a Bill of Material Item is used to make other Manufacture Routings.
- P/O Receipt History: shows Receipt history for each Bill of Material Item including the P/O #, Vendor, P/S #, Received On date, Received By, Receipt #, Wanted On date, Received Quantity, U/M, and Unit Price.
Note
Users can right-click on any Bill of Material Item and open the R/M Inventory screen.
Orders Tab¶
The Orders tab on the Production Inventory screen can be viewed by clicking on the tab.
This tab is useful for viewing all upcoming Orders in the system. Firm Orders will be highlighted in blue, and planned will be in white. The Balance column on the right side of the screen indicates the On Hand Balance minus the quantity of the Orders.
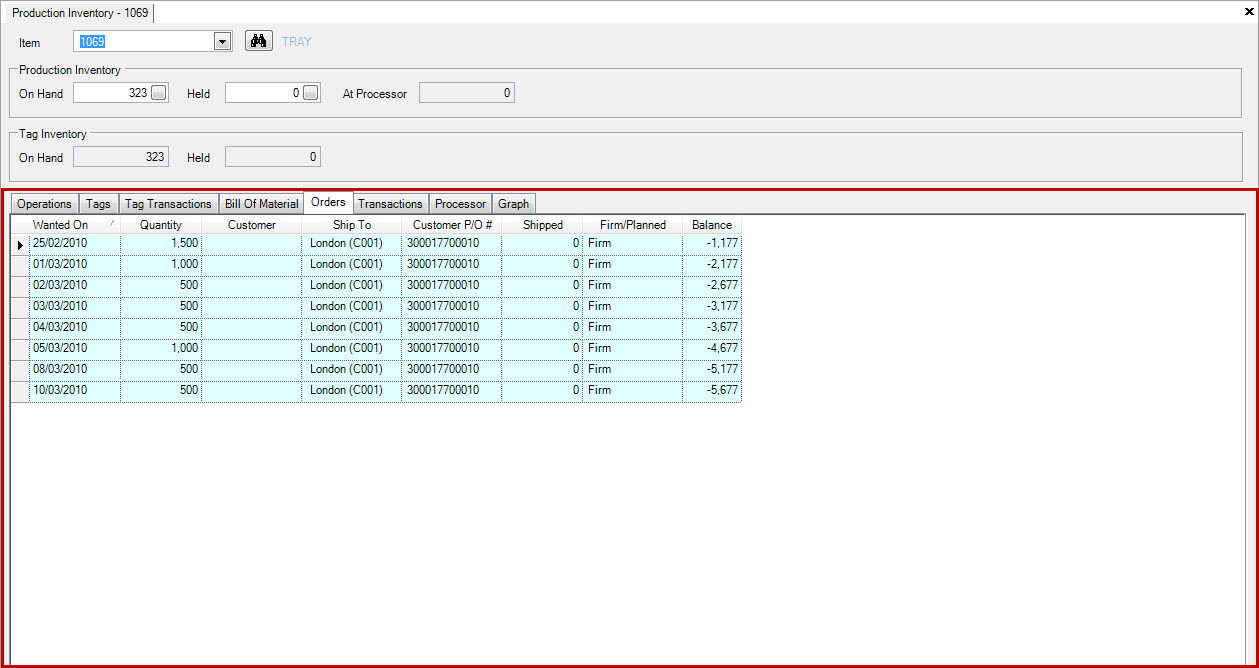
Note
Users can also double-click on an Order row to open the Order detail screen.
Transactions Tab¶
The Transactions tab on the Production Inventory screen can be viewed by clicking on the tab.
This tab is used for determining exactly how you got to an Item’s On Hand Balance. Notice that all of the Packing Slips, Timecards, and Inventory Adjustments are recorded, and the system allows you to open Timecards and Packing Slips directly from this screen. This screen is useful when there is a discrepancy between the Tag and Production Inventory, in determining where the discrepancy occurred.
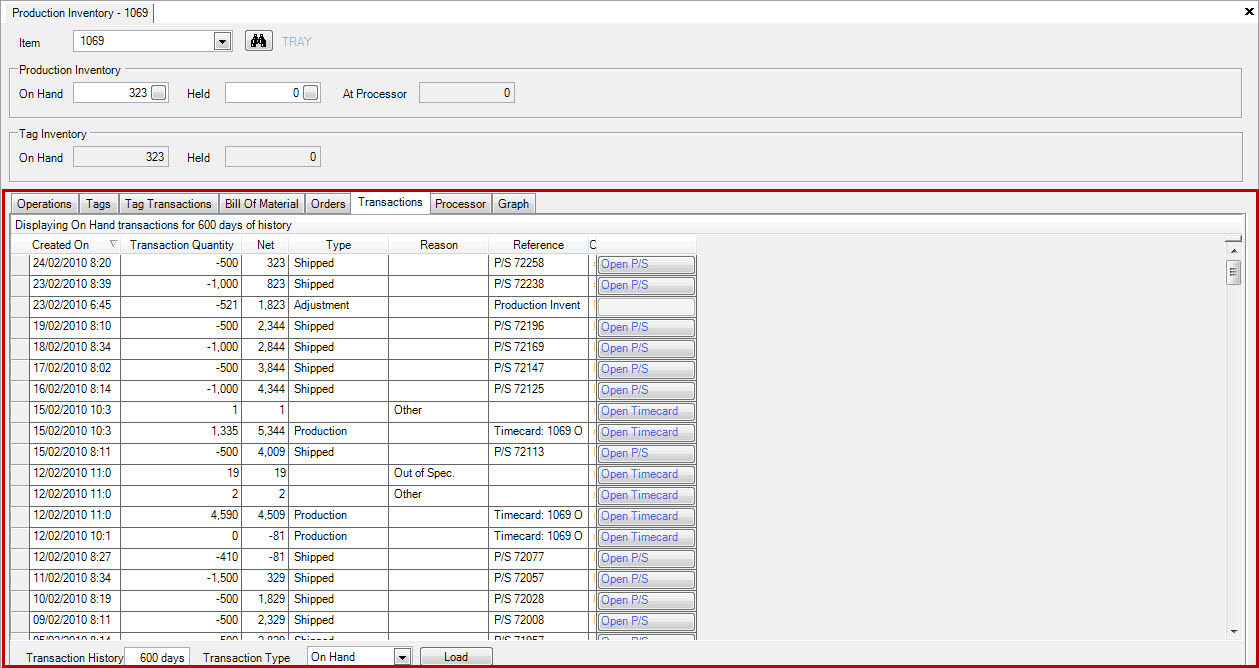
Users also have the ability to view the Transaction History as far back as you wish. Simply enter in the number of days, select the Transaction Type from the drop-down and click on the
button.

Processor Tab¶
The Processor tab on the Production Inventory screen can be viewed by clicking on the tab.
This tab is used to view and adjust Inventory Quantities at a Processor.
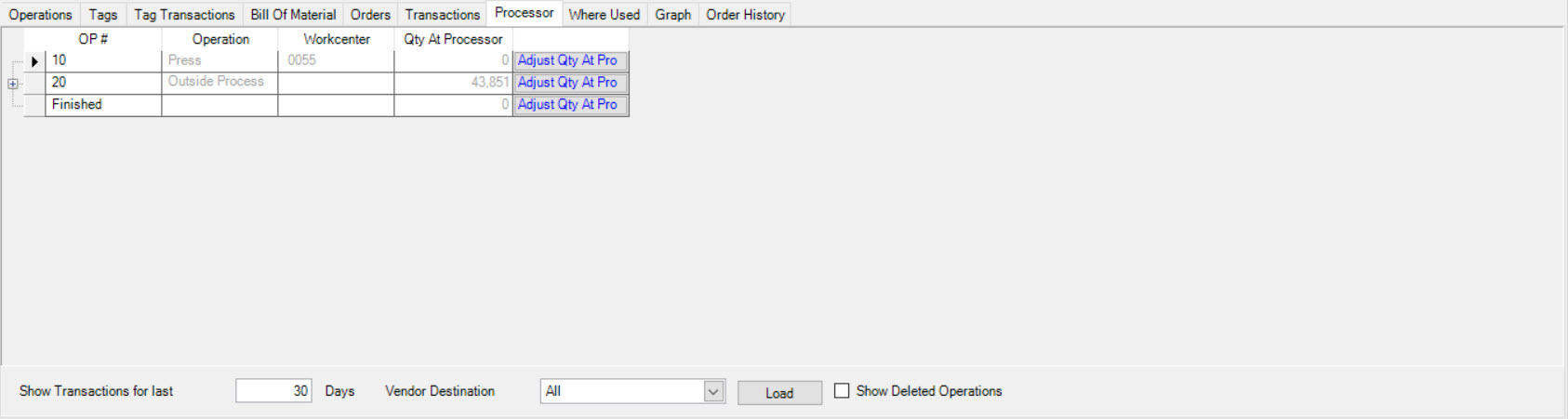
Users can use the plus sign to view the transaction details for an Operation such as when the Inventory was shipped to the Processor (In at the Processor), and when the Inventory was received (Out from the Processor).
To adjust a Quantity, click on the button located in the right column of the screen. This will open the Adjust Quantity at Processor window.
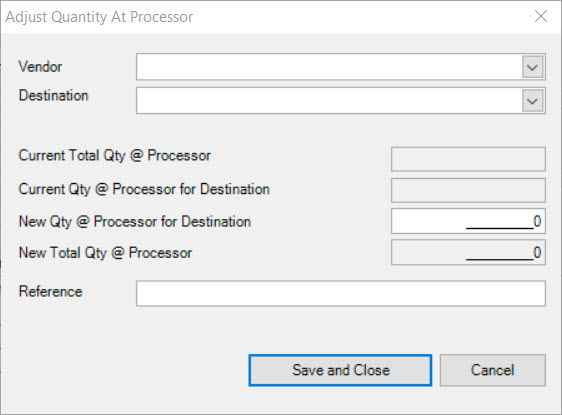
Select a Vendor and a Destination using the drop-down menus, adjust the Quantity, and enter in a Reference. Click on the button
to complete your changes.
Users also have the ability to view the Transaction History as far back as they wish. Simply enter in the number of Days, select the Vendor Destination from the drop-down and click on the
button.

Note
Users can select or de-select the checkbox if necessary.
Where Used Tab¶
The Where Used tab on the Production Inventory screen can be viewed by clicking on the tab.
Note
This tab is only visible when the Item selected is defined as a Component on the Manufactured Routing.
This tab is useful for viewing all items that a component is used for in the system including the Item, Description, OP #, Operation, Quantity Per, and U/M.
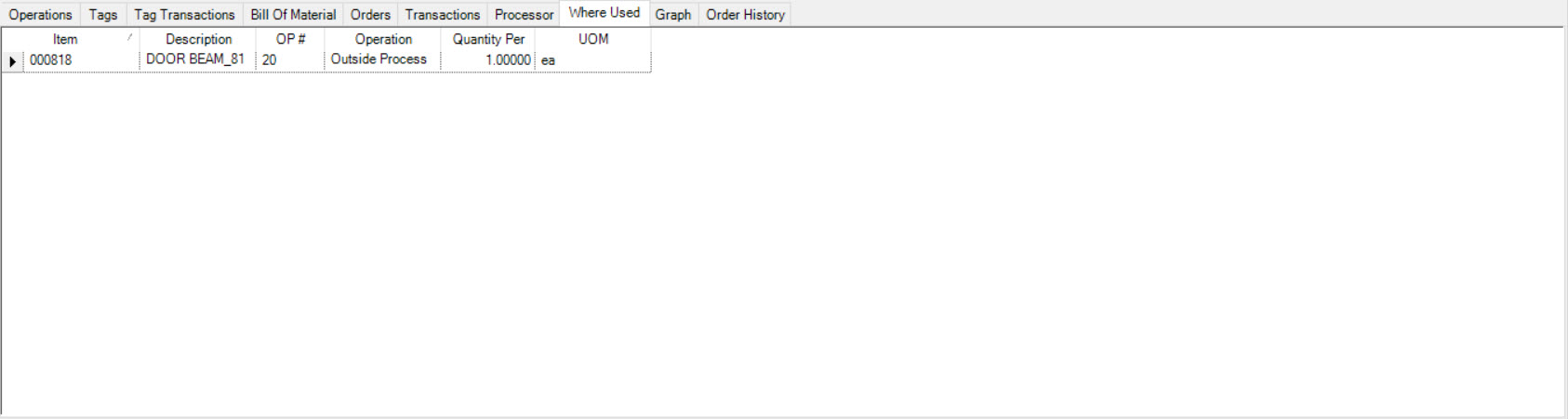
Graph Tab¶
The Graph tab on the Production Inventory screen can be viewed by clicking on the tab.
This tab displays a chart representation of how an Item and all related Items move through the system. If more than one Item is displayed on the screen, the current Item selected will be highlighted in blue.
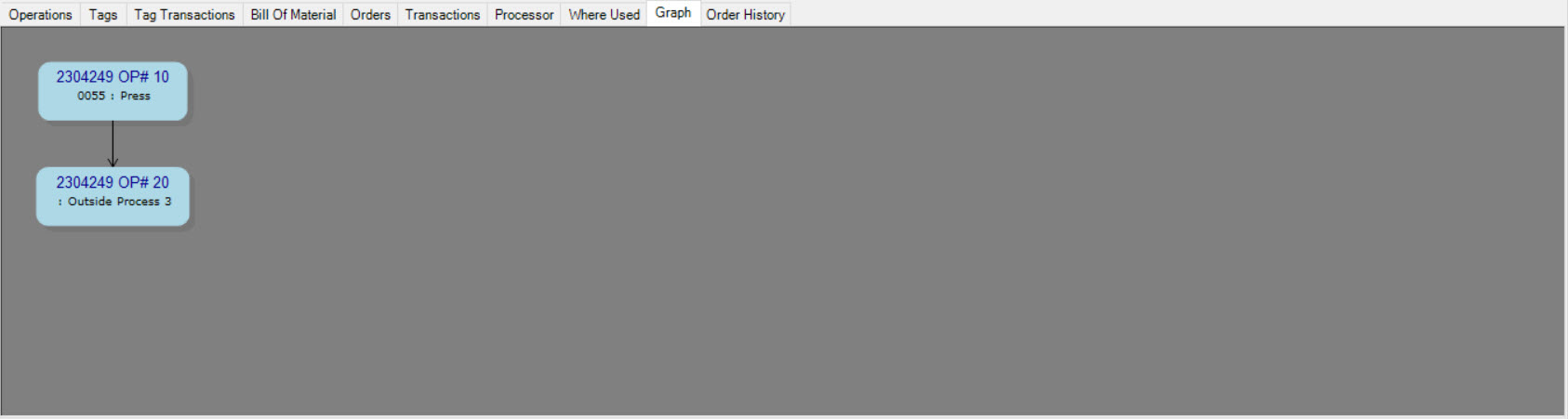
Order History Tab¶
The Order History tab on the Production Inventory screen can be viewed by clicking on the tab.
This tab displays the history of Orders for the Item in the system. If an Order has been shipped against and/or invoiced, users can click on the plus sign to view Packing Slips and Invoices related to an Order. Users can also click on the Order #, P/S, and Invoice to open the actual Order, Packing Slip, or Invoice.
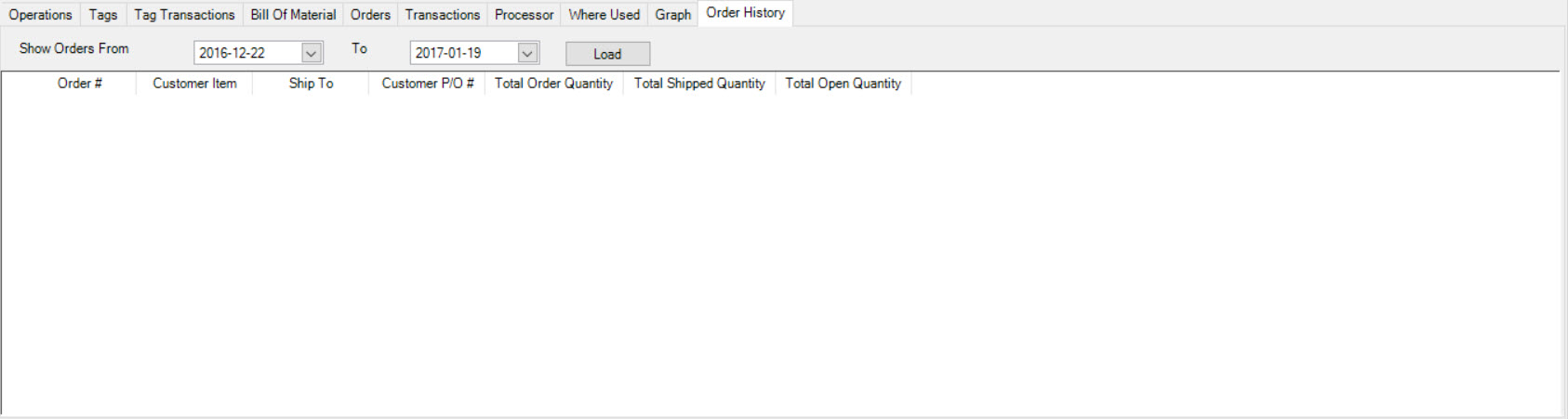
Note
Users have the option to select Show Orders From and To dates. Click on the button once you have selected the appropriate dates.
Projected Inventory¶
The demand is driven by the orders, so the items that require the material are listed on the top level. You have to options: you can drill down to the material on each demand to see how much of the material is needed (you can click on ‘Expand All) or you can switch to ‘Columns’ in which case each item that has a role in the material demand will be listed on it’s own row, as well as the material. Please see the attached screenshots.